Latest news and insights
Ensuring unparalleled glass bottle quality: A peek into Rockwood's quality control processes
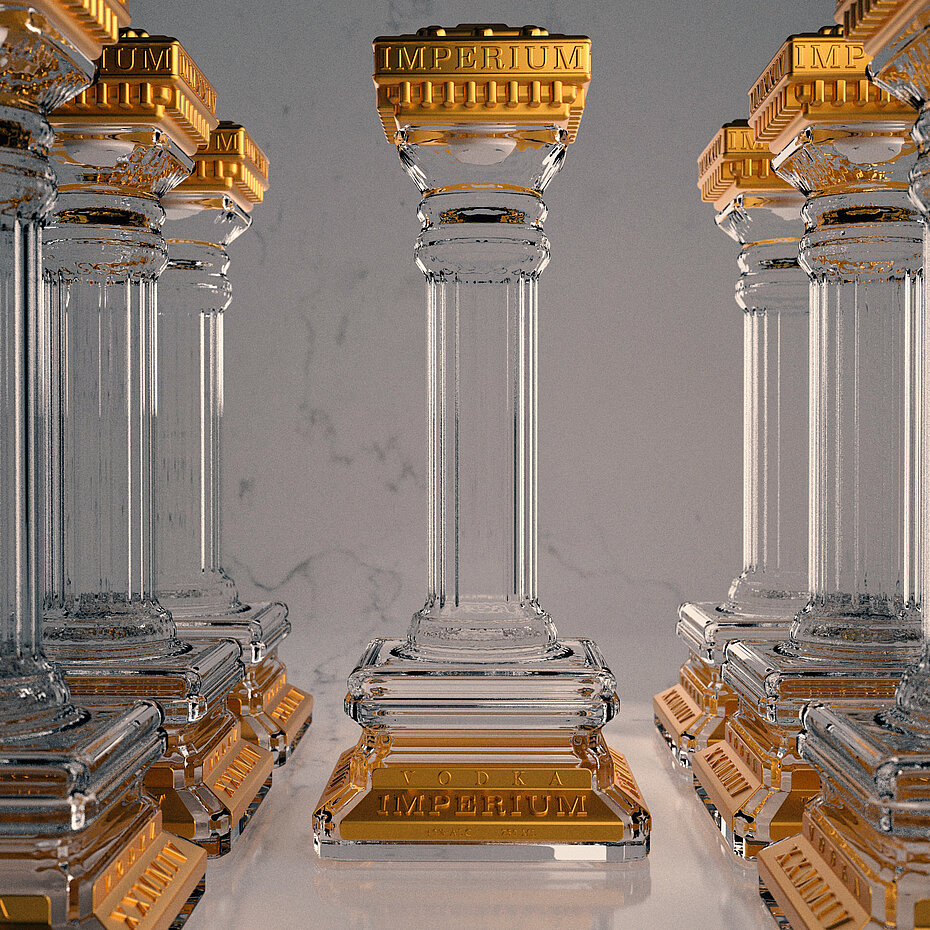
Rockwood Glass has six production lines for glass bottles alone. Despite being based in China, it adheres to European quality control (QC) standards, ensuring that every bottle that leaves the factories is free of blemishes and imperfections.
Rockwood is a 1-stop shop solution for all steps of your custom bottle design, manufacturing, packaging, and delivery. Its factories are known for producing flint and super flint glass bottles of superior quality, thanks to decades of know-how as well as the on-site state-of-the-art manufacturing technology.
Overall, the manufacturing process for glass bottles is complex and requires a high degree of skill and expertise. Rockwood has a team of experienced glassmakers who are dedicated to producing premium bottles that meet and exceed client specifications. By using the latest technology and adhering to strict quality control standards, the company has established itself as one of the leading manufacturers of custom glass bottles, ranking 5th in bespoke bottle creators globally.
The glass bottle production process in a nutshell
During production, glass is heated in a furnace that reaches 1600 degrees Celcius (2900 degrees Fahrenheit), until it becomes molten. The molten glass is poured into the customized mold to take shape. The annealing process of cooling the glass within the mold begins, in order to relieve it of any internal stresses, thus making it more durable. After the bottle has cooled, it is removed from the mold and sent to the finishing station.
Once in the finishing station, the bottle is inspected for any defects or imperfections. If there are any defects, the bottle is discarded and the process is repeated. If the bottle is deemed to be of expected pristine quality, it is sent for further processing. This can include polishing to remove any rough edges, applying a label or design to the bottle, or adding a closure
Quality control processes that set Rockwood Glass apart in China
Our commitment to excellence begins with rigorous quality control processes implemented at every stage of the custom glass bottle's manufacturing journey. Let's delve into the meticulous steps we take to ensure the superior quality of glass bottles for our clients in the spirits and liquor industry:
1. Technical specifications for raw materials
To lay the foundation for quality control, Rockwood Glass establishes comprehensive technical specifications for each raw material employed in our manufacturing process. This includes cullet, the recycled glass used in our production. These specifications outline optimum and normal reject limits for key parameters such as chemical composition and grain size.
2. Supplier certifications
For cullet sourced externally, we prioritize the control of its quality through a formal compliance certificate system. These certificates, ideally integrated into commercial contracts, assure adherence to our technical specifications. Regular supplier audits further ensure familiarity with the supplier's process control methods, enhancing the reliability of the raw materials.
3. Incoming material checks
Upon the receipt of raw materials, whether through local laboratory checks or accredited external labs, we verify their compliance with established technical specifications. The reliance on supplier certificates of conformance and process control information has streamlined this process, reducing costs while maintaining efficiency.
4. Batching, mixing, and melting control
The transformation of raw materials into molten glass is a critical phase. We perform density tests, homogeneity tests, and checks for bubbles, seeds, and stones. These tests assess the glass composition, homogeneity, and potential stress factors, ensuring the quality of the molten glass before further processing.
5. Hot End inspection
As the glass containers take shape at the Hot End, our operators conduct visual and dimensional verifications immediately after the forming process. Regular monitoring of glass weight and prompt defect detection allows us to take corrective actions in real-time, minimizing delays and optimizing the manufacturing process.
6. Cold End quality control
The Cold End phase, dedicated to quality control activities, involves a second inspection by Cold End operators. This step, after annealing and cold end coating, ensures the containers' final quality. The communication between Hot End and Cold End operators is pivotal for defect correction.
7. Automated inspection machines
Our production line features a series of automated inspection machines, including sidewall, base, finish, and multi-inspection machines. These machines use advanced technology to inspect every container produced, guaranteeing a thorough and consistent evaluation.
8. Human visual inspection
To complement automated inspections, our Cold End operators visually inspect containers at regular intervals. This visual assessment helps evaluate the effectiveness of automated inspection machines in capturing visual defects and provides valuable information for process improvement.
9. Final statistical checks
Random samples from assembled pallets undergo a final statistical check to classify defects as critical, major, or minor. This comprehensive inspection ensures that the batch meets our stringent quality standards before reaching the market.
10. Traceability and laboratory testing
We prioritize traceability by assigning sequence-coded labels to each pallet, allowing cross-referencing with inspection records. In our Quality Control Laboratory, we conduct various tests, including thermal shock, internal pressure, and impact tests, to ensure container resistance and compliance with specifications.
11. Continuous improvement and employee involvement
Acknowledging that people are pivotal in our quality control system, we emphasize employee training, knowledge, and skill development. Our Quality Control Manager strategically allocates resources, documented in the Quality Control Plan, to continually enhance our processes.
At Rockwood Glass, our commitment to quality extends beyond manufacturing; it is ingrained in our culture. We believe that by adhering to these stringent quality control measures, we not only meet but exceed the expectations of our customers, delivering custom-made glass bottles of unparalleled quality and craftsmanship.
If you would like to discuss a future collaboration with Rockwood Glass, don’t hesitate to contact us for a free consultation.
Interested in creating bespoke ceramic bottles for a limited or special edition? Then check out the Rockwood Ceramics website here.
Are you ready to embark on a journey of crafting your own private label for a spirit or liquor of your choice? Create your private label with Rockwood!
Rockwood is the largest French-owned glass and ceramic bottle factory in China. It produces over 6 million exclusive bottles for some of the most prominent premium brands in the global spirits and beverages arena, and a further 500+ million classic bottles, annually.